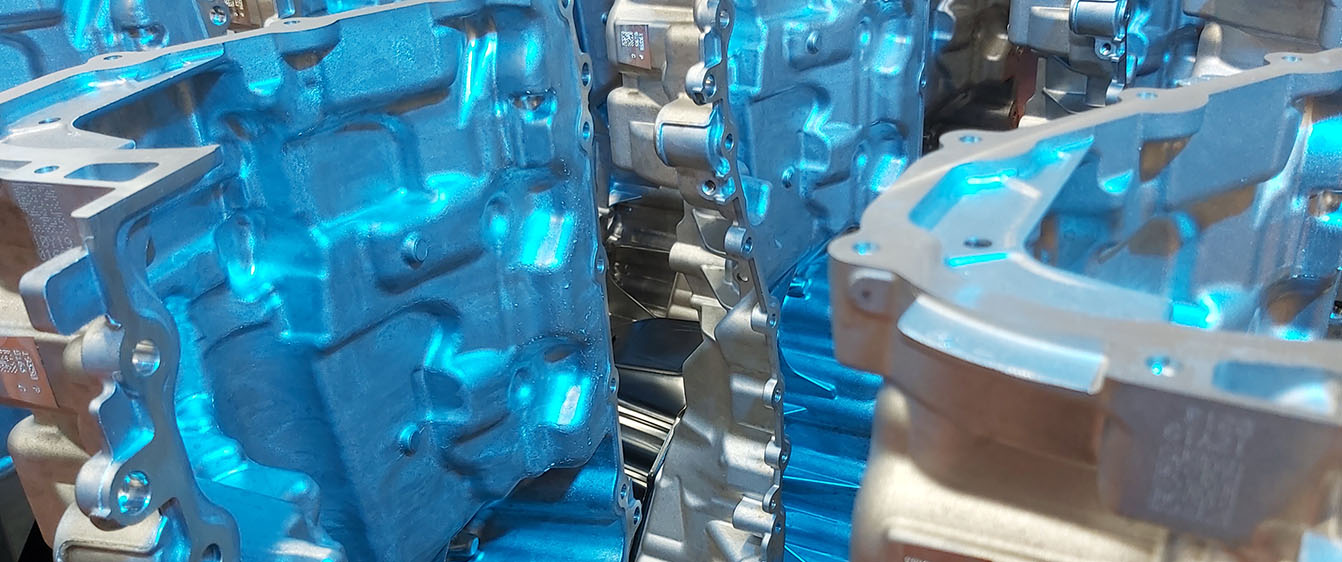
Electric Vehicle Leak Testing
Machines supplied: Electric vehicle leak testing solutions
Clients: Leading global automotive companies
Parts: Various castings, metal components and other associated automotive parts
Overview: With the introduction of main stream, high volume production, electric vehicles earlier this century, TQC became involved with electric vehicle leak testing projects handling associated casting and parts used on this new generation of vehicles. This comes on the back of over 30 years’ experience of leak testing automotive parts.
There are many different components used in electric vehicles, whether this is an all electric, plug-in hybrid (PHEV) or mild hybrid (MHEV), TQC have recently leak tested the following –
- Battery trays
- Electrified drivetrain – Clutch and Transmission cases
- Battery compartment cooling fins
The electric vehicle battery tray project involved a fully automated conveyor based palletised system for presenting trays to a single leak test station. The pressed steel tray was tested by sealing onto the flange area and applying a low test pressure and monitoring any fall in pressure over the test time.
The leak test requirements for this part were quite rudimentary but the same concept of machine can be adapted for finer air decay leak testing and for helium leak testing requirements.
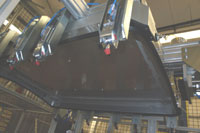
Look at our Case Study of a Battery Tray Leak Test Machine
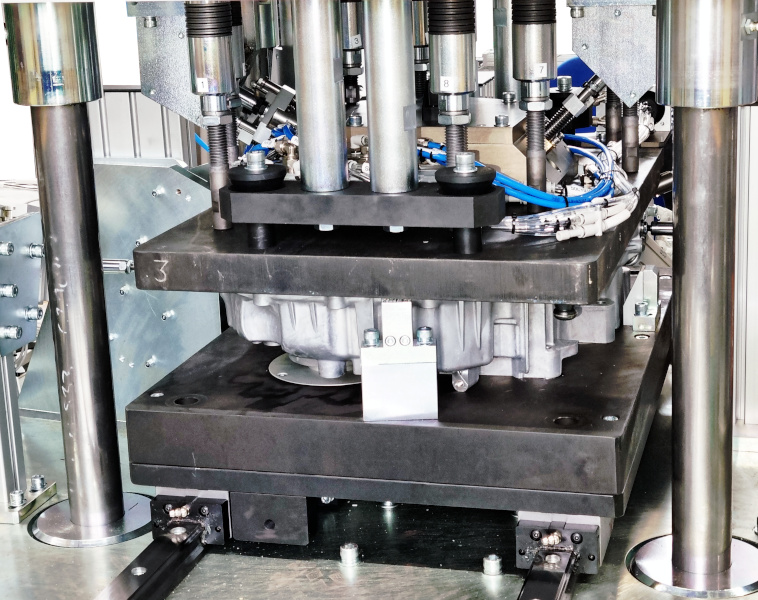
The introduction of electrified drivetrains has meant the complexity of clutch and transmission cases or housings has increased.
There is the need to handle very similar variants of parts to suit the PHEV and MHEV types of electric vehicles.
Generally produced via aluminium die casting, these parts require advanced machining followed by stringent leak testing. Water and oil cavities are common place and these need to be checked to ensure no ingress or leakage during operation.
TQC has integrated over 50 individual seal units into a single leak testing fixture so that a series of cavities can be tested on a transmission housing.
To complement the electric vehicle leak testing equipment, assembly, geometry checking and marking equipment can be included.
Plug insertion is necessary to seal off casting features. TQC integrates automatic plug feeding and assembly with over check leak testing of the inserted plugs.
Pass through characteristics (PTCs) need to be checked so when the finished parts arrived at the engine plant it will fit, TQC automatically checks these features.
For part traceability, a laser marked 2D barcode was added to each casting with readability of the mark automatically checked following application.
As the volumes of electrified drivetrains are now increasing, the handling of the parts between the necessary processes requires automatic robotic handling. TQC integrated 6-axis robots with complex double headed grippers to move castings automatically and efficiently between the leak test, assembly, checking and marking stations.
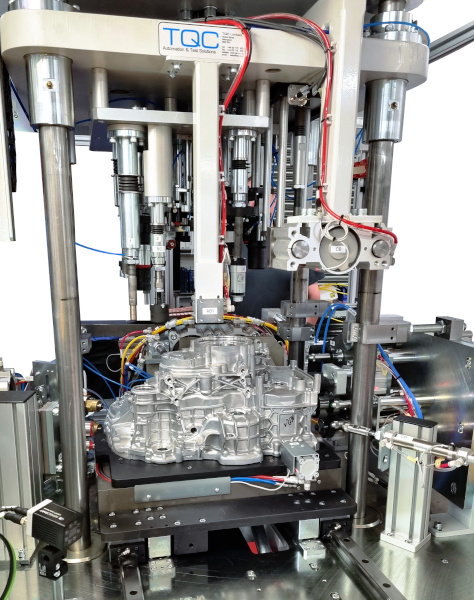
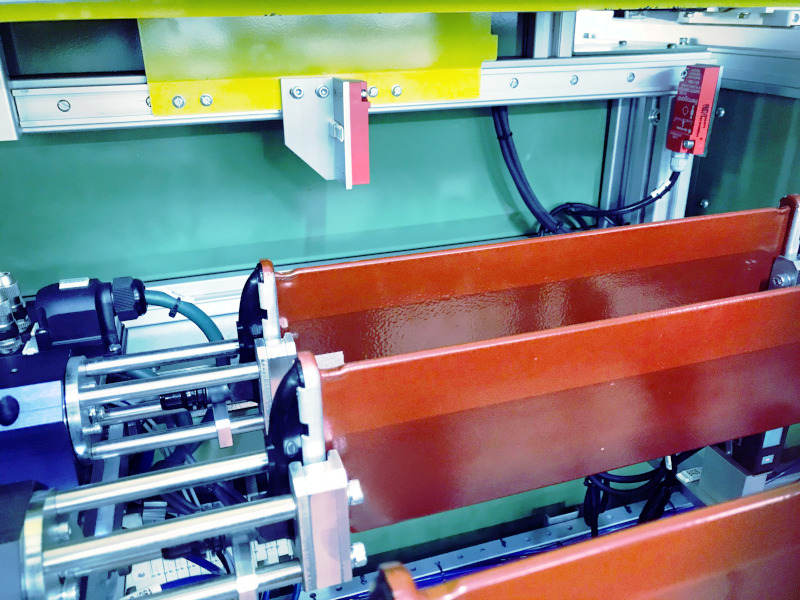
Battery technology is changing rapidly and as part of efficient and safe battery operation cooling is sometimes necessary.
TQC have been involved in the leak testing, inspection and marking of battery compartment cooling fins for a leading worldwide brand. This suite of equipment allowed multiple parts to be processed in parallel so that the high production volumes could be met.
The cooling fins were air decayed leak tested using the TQC MALT unit on several adjustable fixtures. Each fixture included automatic sealing connectors, one at a fixed end, a second on a slide to accommodate part variants. The second system supplied included flow testing, part flatness checking and laser marking of the cooling fins.
If you have an electric vehicle component leak testing or related application that could benefit from TQC’s expertise, please contact us by email or phone via the contact details