
Battery Tray Leak Test Machine
Client: Leading Automotive Vehicle Manufacturer
Part: Electric Vehicle Battery Tray
Machine supplied: Leak Test system with infeed and outfeed conveyors
Overview: This system was designed and manufactured in order to give the customer the ability to carry out battery tray leak testing within their production environment. TQC developed this system alongside the client to allow them to supply quality, tested parts to their customers.
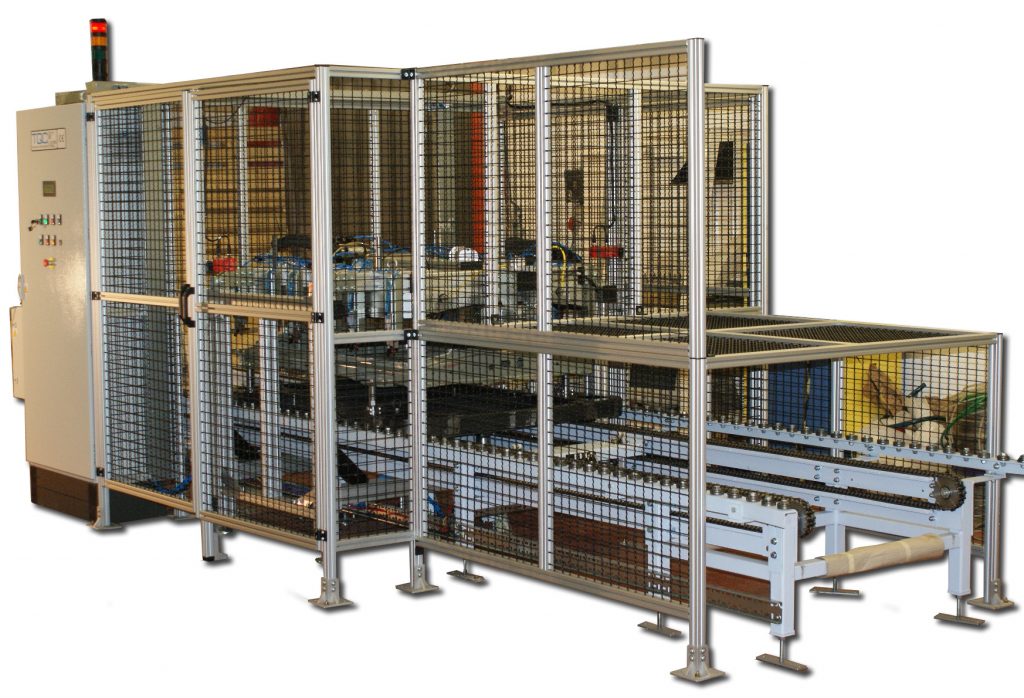
TQC have designed and manufactured a fully automatic solution to provide the final leak test to ensure an automotive battery tray is fit for purpose.
The tray is manufactured from pressed steel components welded together and then hand finished with a sealant to provide the leak tight chamber.
The leak test facility forms a chamber over the tray and clamps a seal down onto the flange area around the upturned lip of the tray. The seal is generated using a ‘P’ shaped neoprene seal.
The battery tray is transported around the conveyor system by a palletised system, each battery tray has it’s own TQC designed and manufactured dedicated pallet.
The test pressure is 16mbar and once the test pressure has been achieved it stabilises and is held for 60 seconds. During the 60 second time period the test pressure must not fall below 14 mbar otherwise the part fails the leak test.
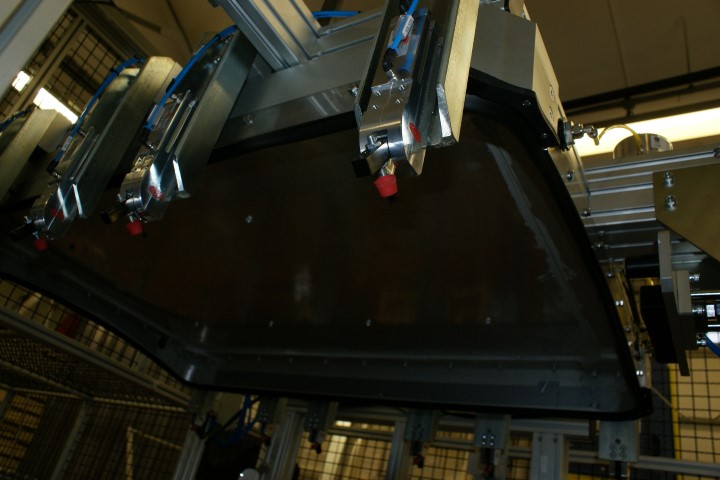
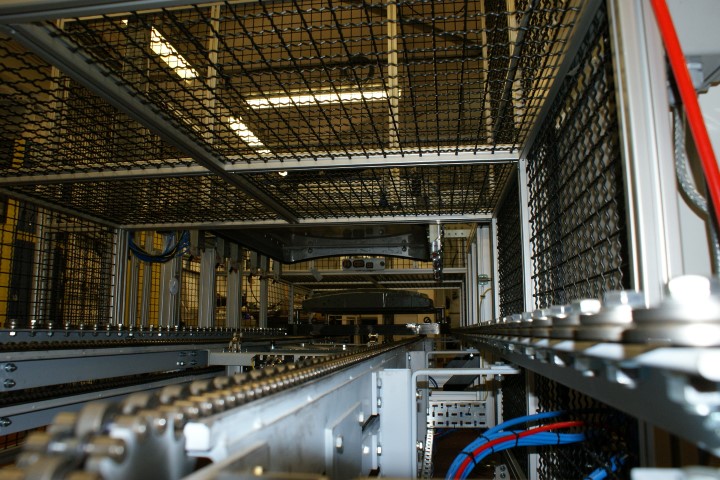
The system is controlled via a PLC with all leak test parameters editable through the HMI.
The system maximum cycle time of 3.75 minutes (225 Seconds), in practice the system throughput is nearer to 90 seconds.
The leak test solution is one of many designed and manufacture by TQC. If you have a part or assembly that requires testing please contact us to discuss further. We have integrated all test methods previously so are well-positioned to offer the optimal solution for your application.
To view a printer friendly format please click below