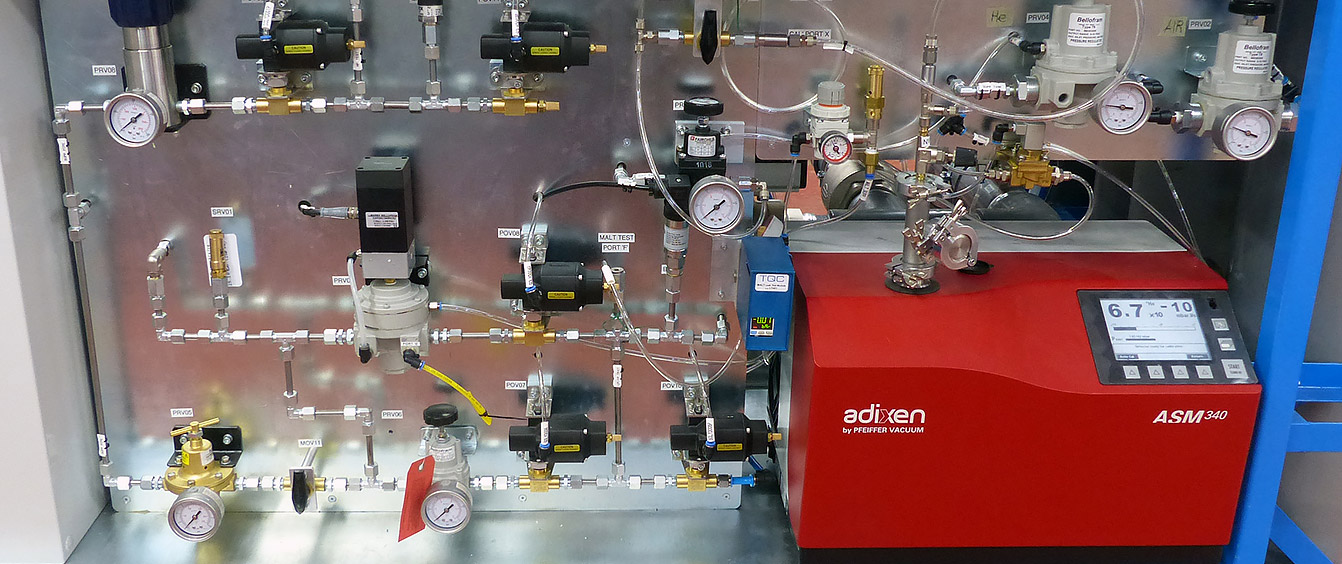
TAMI: Test for leakage identification on aircraft fluid mechanical installations
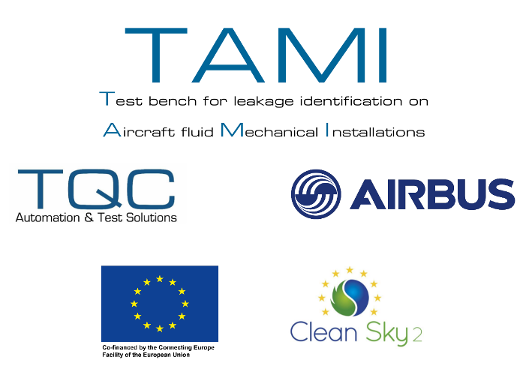
This project has received funding from the European Union’s Horizon 2020 research and innovation programme under the Clean Sky 2 Joint Undertaking grant agreement No 737992.
Aims
The TAMI project is a response to a Clean Sky 2 call for proposals within an overarching topic, Future Leakage Identification Systems (FUGAS), which aims of to develop theoretical models, simulations and methods for the identification of leaks in aircraft systems. These methods are to be practically demonstrated as a general technique and on an aircraft Integrated Technological Demonstrator (ITD).
Specifically the Description of Action (DoA) states that “The project aims to develop innovative methods to make on-ground leak testing more efficient, ecological and faster in aeronautical industry environments, reducing costs, time to market and toxic wastes due to standardization on test procedures and testing using non-polluting means.”
TQC Ltd is the sole beneficiary of the TAMI project, but it is informed by the Topic Manager at Airbus Defence and Space (ADS), and liaises with core partner PASSARO in relation to theoretical models and simulations.
TAMI aims to deliver a “Test Bench” comprising a set of contemporary leak testing systems that can be used to perform practical tests on each of aircraft gas fluid systems, fuel tanks and fuel systems in order to detect and quantify leakages.
The overall objective is to deliver more ecological, more efficient, reliable and lower cost means for leak testing of aircraft fluid mechanical systems.
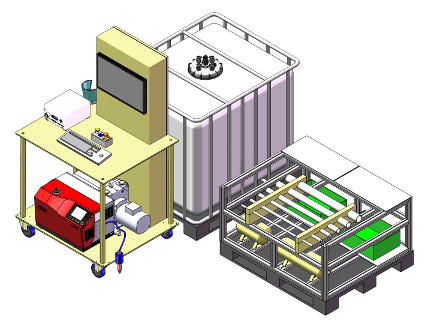
Background to the problem
Currently, many of the leakage tests on aircraft systems are done using the fluid for which this system is designed. Some of these system fluids, like hydraulic fluid and fuel are highly polluting and toxic. Apart from the use of costly fluids, which often have to be wasted, there is a need to prevent major loss of time and construction materials used in assembly due to rework. In addition to the hazardous nature of combustible aviation fuel and the acidic nature of fuels such as Skydrol, they create a slip hazard and containment requirements.
The project action will aim to remove the costly and hazardous liquids from the testing regime for aircraft fluid systems and components where possible by substituting the in-service fluid with a test gas. This means replacing aviation fuel, Skydrol and other expensive liquids with compressed air, a mixture of hydrogen and nitrogen, or helium (balloon gas) test gases. In some instances, the test gas can be recovered to reuse in subsequent test cycles.
There are many leak test methods. The selection of an appropriate leak test method is informed by many parameters such as the volume of the system part, the required test pressure, sensitivity, reliability, location of leak and the testing environment. In order to provide choice and flexibility, TAMI proposed a concept of a single test bench engineered with the versatility to perform a selection leak tests appropriate to aircraft systems. This bench would also be readily manoeuvrable in aircraft production area.
Work Packages
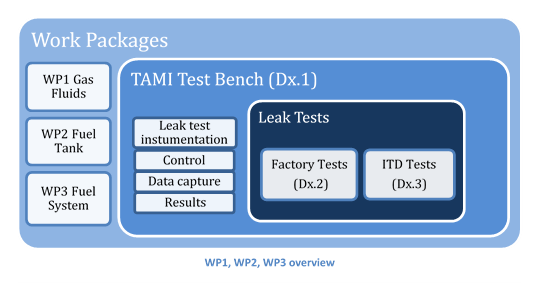
The work packages are constructed in accordance with to three aircraft systems identified in the project call. Specifically, the Tests for leakage Identification on Aircraft fluid Mechanical Installations (TAMI) will develop and demonstrate modern methods and strategies for leak testing aircraft gas systems (WP1), fuel systems (WP2) and fuel tanks (WP3).
The structure of each work package WP1, WP2 and WP3 is the same; the difference is in the application area (gas fluids, fuel tanks, fuel system). In a nutshell the five tasks for each WP system are:
- Specification: to prepare a set of laboratory and aircraft tests
- Assemble leak testing equipment and representative aircraft structures; and carry out laboratory tests;
- Carry out the developed tests on the Aircraft Integrated Technical Demonstrator;
- Compile, compare and summarise the test results;
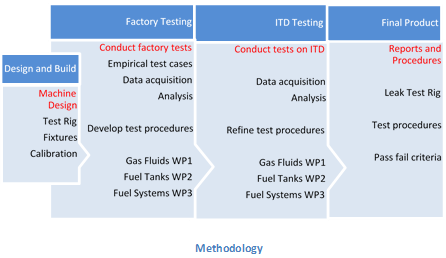
Summary of Activities to M15
In the initial stage of the project the beneficiary (TQC Ltd, UK) established a working relationship with the Topic Manager, and other partners working on the State of Art and theoretical considerations. At the TAMI ‘kick-off’ meeting the Topic Manager gave an overview of the synergies between the theoretical and practical paths of the project. There were presentations by the theoretical path (PASSARO) and by TQC as the sole beneficiary of TAMI.
The main technical effort during this period was to get a more detailed understanding of the nature of the target systems on the aircraft to be tested for leakages. The engineering team at TQC completed a first cut design of the TAMI test bench and concept designs for aircraft representative structures for the practical laboratory tests. A draft version of the specifications for laboratory test was completed, including a template for recording test results. Detailed engineering designs have been completed for the TAMI test bench and the target volumes to be used in laboratory tests. The TAMI test bench will comprise of instrumentation and interfaces for conducting leak tests using tracer gases and pressure decay.
Additionally, TAMI designed and assembled bespoke apparatus to test leakages through pinhole orifices. The objective is to corroborate the leak rates derived by the theoretical path with the aim of establishing the correlation between liquid (fuel) and (test) gas leakages.
Summary of Activities to M27 (end of project)
The TAMI Bench has been fabricated, assembled and factory tested. It brings together in one place the test methods that can be applied to each of aircraft gas fluid systems (WP1), fuel tanks (WP2) and fuel systems (WP3) in order to detect and quantify leakages. It comprises instrumentation to: sequence and control different types of leak test methods; monitor and capture data during the tests; and record the results.
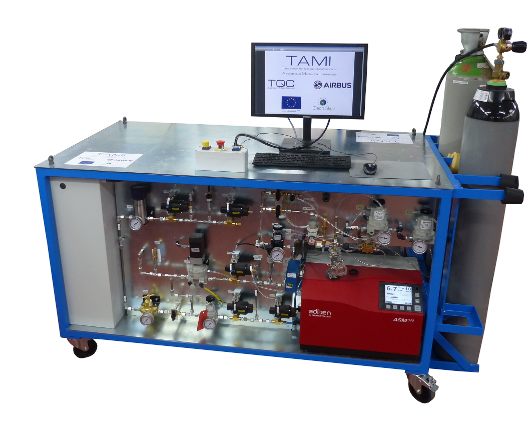
The tests methods supported are tracer gas (Helium) detection, pressure decay, and differential pressure change. The pressure decay method is only sensitive enough for aircraft pipe systems with small to medium volumes, but it is also used with larger volumes to preclude a gross leak in the test cycle for tracer gas detection.
Factory testing was carried out to develop the procedures for the different leak test methods. This is a relatively complex process that requires a deep understanding of fluid mechanics and the leak test cycle. A significant part of the development of test procedures involved calibrating the instrumentation, refining the software control programs, and configuration of the leak test cycle and software to achieve an acceptable level of sensitivity, reliability and repeatability. This process had to be completed for each test method and aircraft system.
The results of the tracer gas method demonstrated that the TAMI bench could be used with a Helium sniffer to detect leaks at proposed sensitivity. An exercise comparing Helium detection with Bubble growth was carried out showing the correlation between them demonstrated the Helium method is more accurate as the leak rate gets smaller.
Finally, TQC‘s own Micro Application Leak Test (MALT) instrument, which is incorporated in the TAMI bench, was used for the (differential) pressure decay method. This is very accurate for small volumes. The MALT unit is best used to ensure components are leak-tight before assembly.
TAMI factory tests at TQC were conducted using volumes that are representative aircraft structures. These tests demonstrated the feasibility of the tests, and established the leak test parameters and control program configuration in preparation for testing the aircraft systems on the AIR ITD.
Testing on an aircraft in a real environment
To demonstrate the TAMI bench in a real environment it was transported to the Airbus Defence and Space (ADS) site in Seville. Leak tests were carried out on the fuel tank, fuel pipe and fire extinguisher system of a wing and centre fuselage section of a C295 type aircraft. The factory tests were adapted to the volumes and components present in the aircraft.
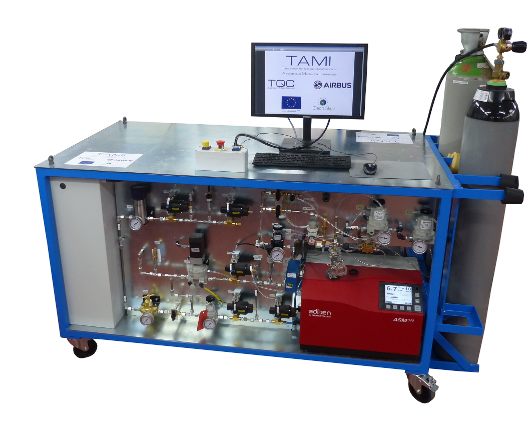
Most of the effort was directed in validating the tracer gas leak testing method. For example, the steps in the use-case of the aircraft fuel tank were broadly:
- Pressurise to ‘gross leak pressure’
- Gross leak pressure decay test
- Complete pressurization of the test volume introducing the correct proportion of helium to achieve the pre-calculated concentration (an integrated fan circulates the gases to ensure a homogeneous gas mixture fills the fuel tank)
- Allow the system to stabilise
- Check the helium concentration to ensure it matches expectation
- Search for leaks with helium sniffer probe (see image)
- Control software maintains test pressure and helium concentration with automatic top-ups.
The instrumentation is calibrated so that meaningful leak rates can be calculated from the readings. Data is continuously logged for post-test analysis if required.
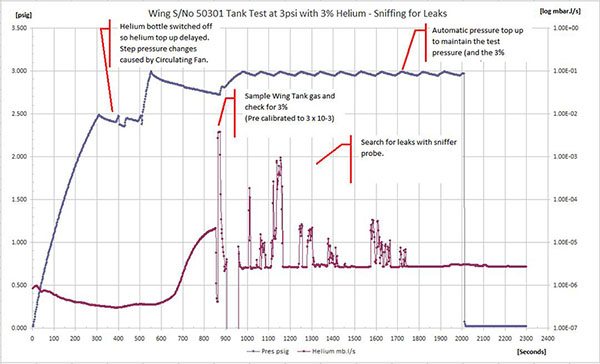
This test revealed a number of leakages from the wing. They were confirmed visually by bubble formation when soap solution was applied around the joints where the leaks were detected.
Helium Leak Detection Bubble Formation
The tests at ADS demonstrated the feasibility of the TAMI bench as a compact unit that can be used flexibly to test a range of aircraft systems. The duration of the tests are much shorter than current tests some of which require visual inspection of components after filling them with liquid fuel (or substitute). In addition, the helium and pressure decay tests methods are clean, economical and more sensitive.
It can be concluded that the central aims of the TAMI project have been demonstrated.
Impact
Clean Sky 2 aims to achieve minimal impact of aviation on the environment through key innovations and to exploit synergies between Clean Sky technologies and those matured outside Clean Sky with potential complementary benefits. The ITD’s allow the maturing of verified and validated technologies from their basic levels to the integration of entire functional systems.
The impact of TAMI is to deliver more ecological, more efficient, reliable and lower cost means for leak testing of aircraft fluid mechanical systems.
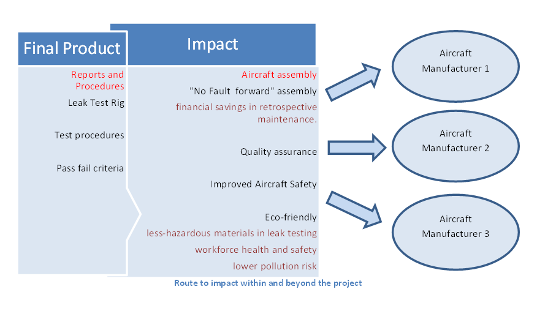
In recent years, the occurrence of oily pools from dripping automotive engines has reduced. This is, in part a result of the more rigorous testing regimes during the original assembly of the vehicle and of its spare parts. In the pharmaceutical and medical device sectors, the potentially lethal nature of leakage in some instances also requires rigorous testing regimes for leakage. TQC has played a significant part in this improved performance of leak testing in these sectors. The TAMI project has applied the techniques used in the automotive and pharmaceutical/medical device industries to the aerospace industry.
Indeed, TQC has in the past year designed and commissioned a reliable and ‘clean’ leak testing system for components in a ‘no-faults forward’ jet engine assembly process. The company has already reported very significant financial savings (€3M) as a result of these pre-emptive tests.